Stay updated
At Teijin Aramid, we’ve got great stories to tell about the way our technologies, products and solutions are making a meaningful difference to people’s lives. Read our latest news to learn more.
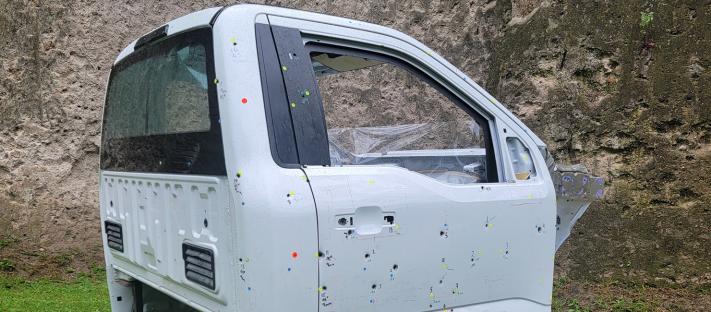
Partnering with SAFECO® sets new standards in performance and innovation
SAFECO® partners with Teijin Aramid to deliver superior ballistic protection using Twaron® fibers, offering high performance and safety for armored vehicles. Read more about how this collaboration is driving innovation.
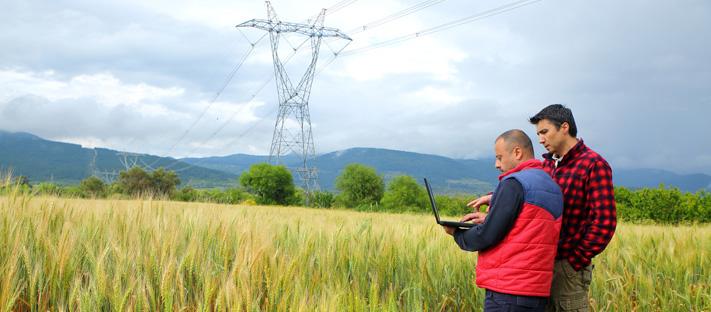
Advancing sustainability of optical fibers & cables
Together with our valued partners Borealis, Covestro, Heraeus, Nextrom, and Umicore, we are pleased to announce the launch of the Sustainable Optical Fiber and Cable Industry Alliance (SOFIA), an initiative to promote sustainability in the optical fiber and cable sector.
Teijin Aramid wins Innovation Award for Twaron® with recycled content
Teijin Aramid has been honored with the Tire Technology International Materials Innovation of the Year Award. This prestigious award is voted on by a panel of over 25 tire industry experts and recognizes industry-leading advancements.

Teijin Aramid and FibreMax Drive Floating Wind Innovation
In a stride towards sustainable energy, Teijin Aramid and FibreMax have secured a €4 million subsidy from the Just Transition Fund Groningen-Emmen (JTF) for our groundbreaking Floating Wind project. This initiative marks a significant advancement in renewable energy.
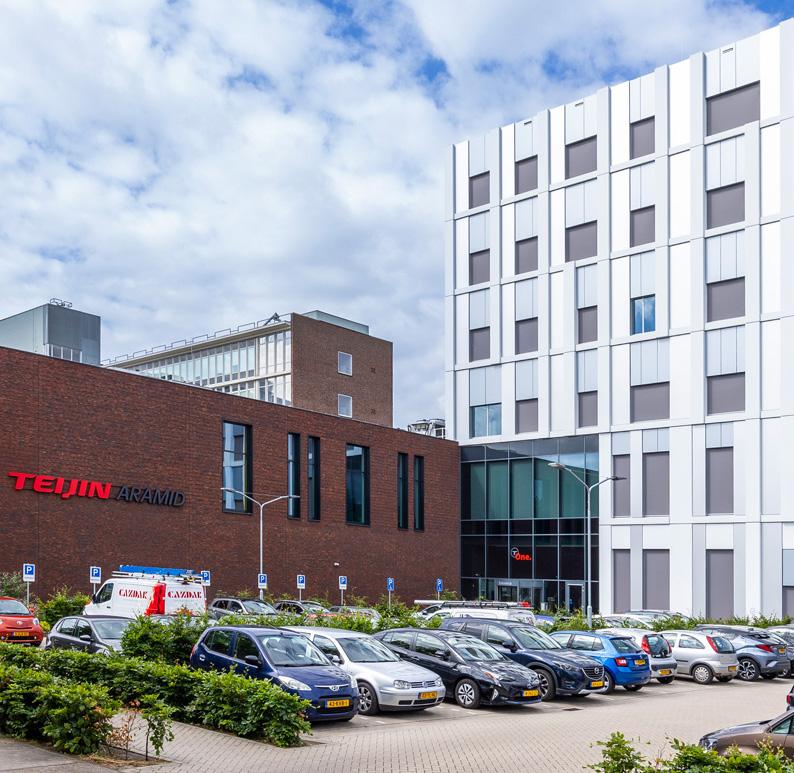
Contact
Get in touch
No matter your question or request, we’ll connect you with the right expert. Fill in the contact form, and we will get in touch with you as soon as possible.